RADOX® CABLE TECHNOLOGY
RADOX® stands for "radiation X-linked" and describes the process of crosslinking thermoplastic polymers by means of electron beams. Our supplier Huber + Suhner has been using this technology, which was developed in-house, successfully since the 1970s to achieve notable improvements in the thermal, mechanical, and chemical properties of the cable insulation material. RADOX® cables do not melt, possess better abrasion resistance and greater cut resistance than conventional cables and, even with thinner insulation, are much more resistant to various environmental factors.
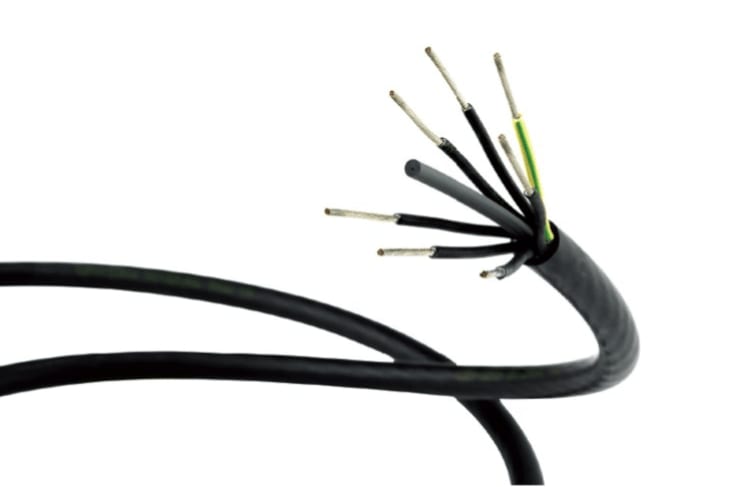
Overview of advantages
Thermally
- RADOX® does not melt
- No drip-off from insulation material in case of short circuit
- Extended lifetime at lower temperature
- Less shrinking of insulation material in higher temperature
- Better heat ageing performance
- Better fire performance
Mechanically
- Thinner insulation due to improved mechanical and chemical resistance properties
- RADOX® withstands temperature peaks
- Improved abrasion resistance
- Improved cut through resistance
Chemically
- Better environmental resistance (UV, ozone, weathering, water, salt water etc.)
- Better resistance against liquids (oil, battery acid, grease, AdBlue, solvent resistance and other chemicals)
Do you need help?
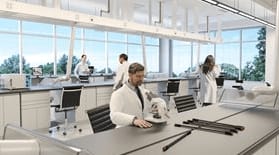
Development
Our supplier Huber + Suhner develops the RADOX® materials themselves. The cables are designed and manufactured in accordance with international standards, as well as customer-specific requirements. Decades of experience, continuous quality checks and extensive laboratory tests guarantee the highest quality standards.
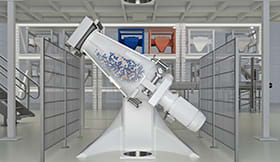
Plastic mixture
To meet rising demand, Huber + Suhner built a new mixing plant at the Pfäffikon site in 2011 for the preparation of the mixtures. This highly automated production facility manufactures all the RADOX® variants for the different areas of application. In the extruder, the mixture is ultimately applied to the conductor material by means of melt extrusion.
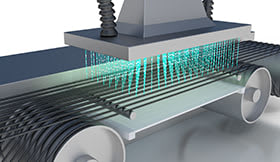
Elektronstråle-tverrbinding
RADOX®-kablene ferdiggjøres ved bruk av elektronstråle-tverrbinding. Kabelen føres gjennom tverrbindingssystemet på en kontrollert måte. Stråling med høyenergielektroner endrer den kjemiske strukturen til polymeren over hele omkretsen til kabelen. Molekylene til polymeren blir deretter tverrbundet, noe som avslutter prosessen.